The wallies at DeWally, bless 'em, elected to use a 150mm M6 carriage bolt and an ordinary nut to cope with the tension on the blade. Well it strips the thread on the bolt over time, doesn't it? About once every two years in fact. And DeWalt charge ten whole pounds sterling for a replacement. Naturally I only did that once before I learnt my lesson. Instead I did two things; first, the purchase of a connecting or double nut to help spread the load across more threads - luckily it fits easily in the tensioning knob.
Secondly, should you find yourself in a similar situation, first purchase a 150mm long M6 carriage or coach bolt. Realise the threads as provided aren't long enough so thread them a little further with the correct size of die. You can see from the defunct bolt on the left it's the "proper" threads that give up, not the self-tapped ones.

The tricky bit is dismantling the bolt from the saw without having bearings and washers cascading about your ears. The blade is removed first, then you have to undo the tensioning knob while supporting the weight of the wheel and holding the bolt up in your other hand, and ultimately balancing the small tower of washers and bearing washers on top of the spring while you remove the tensioning knob before swiftly gathering up said tower before letting the bolt slip from the wheel. Whatever you do, you mustn't let the bolt drop out before you've corralled the washers or you'll be on your hands and knees looking for them for a week. Sound complicated? Believe me, it's much worse than it sounds...
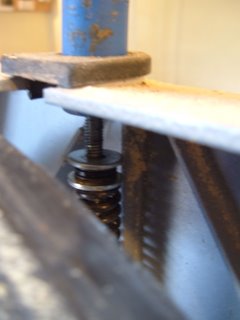
But possibly not as bad as putting it all together again... Generally I drop at least one thing as I do so - carefully feeding the washer/bearing tower piece by piece onto the bolt, gradually feeding it upwards as I also support the wheel's weight - and this time it was the tensioning knob. Usually that means dismantling everything again, bending down to retrieve the knob and starting again. Bless the apprentice - as is their purpose in life, he was there to pick it up for me! So instead of prolonged cursing it all went swimmingly first go, and the blade was tracking and the guides set up in no time. And best of all he gets to do it next time instead of me. Huzzah!
I reckon could get used to the idea of having an apprentice...
Don't let him get too good, Alf, or Alan Sugar will be offering him a job......
ReplyDeletePaul Chapman